Business
Why Injuries Are More Common in Packaging Areas
A business’s packaging and shipping area can see more injuries than any other department. What is it that makes these necessary tasks so hazardous?
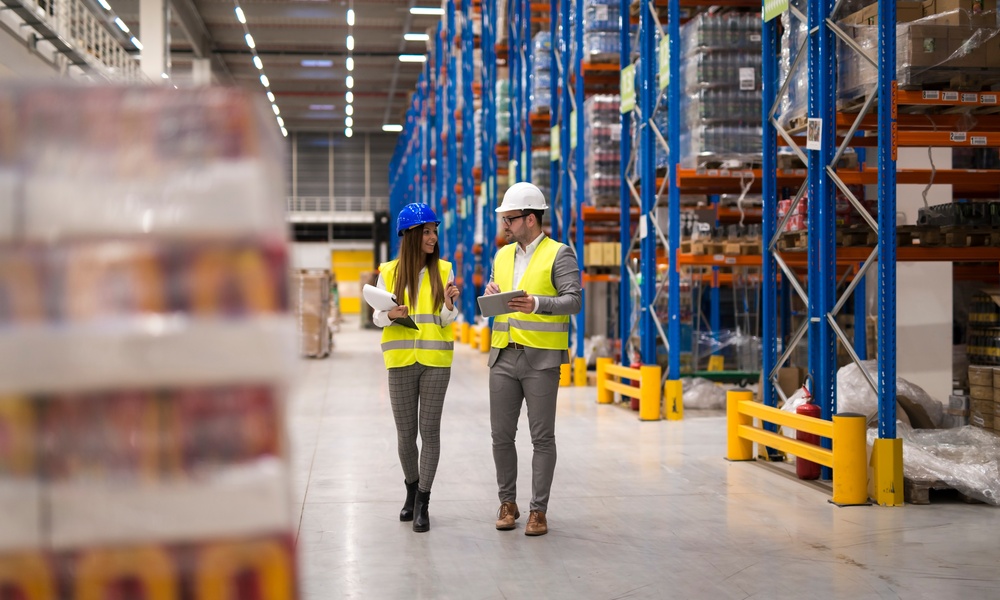
Efficient packaging is the backbone of any business’s supply chain, yet it’s also one of the most hazardous environments in the workplace. Why injuries are more common in packaging areas often comes down to the combination of repetitive motion, heavy machinery, and fast-paced tasks. For business owners, mitigating these risks isn’t just about safety; it’s about protecting productivity and profitability.
The Physical Toll of Repetitive Movements
Packaging work requires repeated movements, like lifting, bending, and reaching. Over time, these actions strain muscles and joints, leading to injuries such as sprains and tendonitis. A single physical misstep can have a ripple effect, sidelining workers and slowing operations. When employees face tasks that demand precision but lack ergonomic support, the risk for strain-related injuries increases significantly. Ensuring better ergonomics can minimize these risks, but it’s not a complete solution.
Heavy Equipment and Machine Hazards
Packaging areas often rely on machinery like conveyor belts, forklifts, and shrink wrappers. While this equipment boosts efficiency, it can also introduce dangers if workers remain involved in the process. Without proper training or safety protocols, workers face risks such as crushed fingers, collisions, or entanglement injuries. Switching to automated options can distance workers from these hazards. For example, palletizers and manual labor each have their pros and cons when it comes to product packaging, but using automatic palletizers removes the risk of many of these machinery-related incidents. Automation doesn’t just save time in packaging departments; it builds a safer work environment.
Tight Deadlines Create Unsafe Practices
Packaging areas often operate under tight schedules to meet high demand. This pressure can lead employees to cut corners on safety to hit quotas or finish faster. Skipping proper lifting techniques or rushing around heavy machinery raises the chance of accidents. Encouraging a culture that prioritizes safety over speed is crucial for reducing workplace injuries. Safety and efficiency must go hand-in-hand if businesses want to protect workers without sacrificing output.
Limited Staffing Exacerbates Risks
Many businesses face labor shortages, forcing fewer workers to handle more tasks. This increases fatigue, mistakes, and burnout, which put employees at higher risk for accidents. Even highly skilled staff struggle to maintain safety when overloaded with responsibilities. Incorporating automated solutions alongside existing staff levels can bridge these gaps and prevent overworked employees from making costly errors.
The Bottom Line
Packaging areas are the heart of many business operations but can also be their most hazardous zones. The reasons injuries are more common in packaging areas boil down to physical stress, tight deadlines, equipment hazards, and understaffing. Business owners must prioritize safety by improving ergonomics, training staff, and integrating automation where possible. Productive packaging environments thrive on efficiency and proactive safety measures, ensuring both workers and workflows remain injury-free.
